Descubra os princípios, regras e tabelas padronizados que permitem tomar decisões informadas sobre tolerâncias para qualquer cenário. Atualize sua compreensão da ISO e revolucione sua engenharia de precisão.
O que é a ISO?
O sistema padronizado pelo ISO (International Organization for Standardization) é constituído por uma série de princípios, regras e tabelas que permitem a escolha racional das tolerâncias adequadas para cada caso.
O sistema ISO considera todas as dimensões compreendidas entre 1 e 500mm, subdivididas em grupos para efeito de cálculo da unidade de tolerância (i).
GRUPO DE DIMENSÕES | |
---|---|
0 até 1mm | > 50 ≤ 80 |
> 1 ≤ 3 | > 80 ≤ 120 |
> 3 ≤ 6 | > 120 ≤ 180 |
> 6 ≤ 10 | > 180 ≤ 250 |
> 10 ≤ 18 | > 250 ≤ 315 |
> 18 ≤ 30 | > 315 ≤ 400 |
> 30 ≤ 50 | > 400 ≤ 500 |
A unidade de tolerância é o µm e seu cálculo é baseado na média geométrica (MG) de dois valores extremos, como mostrado na fórmula a seguir:

Graus de tolerância
Fabricação das peças de um paquímetro ou de qualquer outro instrumento de medição deve conter erros menores que as peças de um motor de automóvel, que por sua vez deve conter erros menores que as peças de uma betoneira.
Erros menores implicam tolerâncias menores e melhor acabamento superficial.
O sistema ISO estabelece 18 qualidades de trabalho (graus de tolerância) designadas IT 01, IT 0, IT 1, até IT 16 (I de ISO e T de Tolerância) para atender às diversas finalidades de construção de peças.
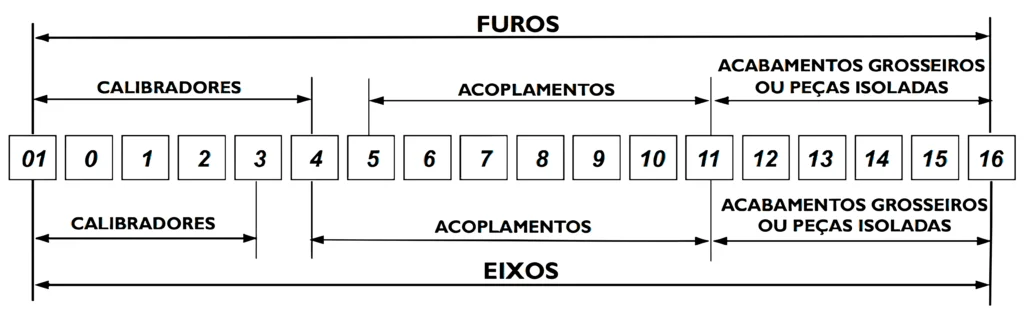
Valores das tolerâncias fundamentais
Os valores das tolerâncias fundamentais, a partir da qualidade IT 5, são calculadas em função da unidade de tolerância “i”.
Qualidade (IT) | 5 | 6 | 7 | 8 | 9 | 10 | 11 | 12 | 13 | 14 | 15 | 16 |
---|---|---|---|---|---|---|---|---|---|---|---|---|
TOLERÂNCIA | 7i | 10i | 16i | 25i | 40i | 64i | 100i | 160i | 250i | 400i | 640i | 1000i |
Tipos de sistema e respectivas categorias de ajustes
Sistema furo–base (SFB)
É o sistema pelo qual, para todas as categorias de ajuste, a dimensão mínima do FURO é igual à dimensão nominal. O número de ajustes possíveis e que satisfaçam as condições de operação do conjunto é extremamente elevado. Para maior simplicidade, sempre que possível, deve ser adotada a posição H do campo de tolerâncias para FURO, obtendo-se, a partir destes, as tolerâncias do EIXO.
Dimensão nominal (mm) | FURO H7 (µ) | EIXOS (µ) | |||||||||
---|---|---|---|---|---|---|---|---|---|---|---|
Acima de | até | f7 | g6 | h6 | j6 | k6 | m6 | n6 | r6 | s6 | |
50 | 65 | +30 0 | -30 -60 | -10 -29 | 0 -19 | +12 -7 | +21 +2 | +30 +11 | +39 +20 | +60 +41 | +72 +53 |
65 | 80 | +62 +43 | +78 +59 | ||||||||
80 | 100 | +35 0 | -36 -71 | -12 -34 | 0 -22 | +13 -9 | +25 +3 | +35 +13 | +45 +23 | +73 +51 | +93 +71 |
100 | 120 | +76 +54 | +101 +79 | ||||||||
120 | 140 | +40 0 | -43 -83 | -14 -39 | 0 -25 | +14 -11 | +28 +3 | +40 +15 | +52 +27 | +88 +63 | +117 +92 |
140 | 160 | +90 +65 | +125 +100 | ||||||||
160 | 180 | +93 +68 | +133 +108 |
Sistema eixo–base (SEB)
É o sistema pelo qual, para todas as categorias de ajuste, a dimensão máxima do eixo é igual à dimensão nominal. Utiliza a letra h para o seu campo de tolerância.
O sistema EIXO-BASE possui poucas aplicações. Por exemplo:
- ajuste de diversos cubos no mesmo eixo;
- montagem de anéis externos de rolamentos;
- ajustes de furos com eixos calibrados etc.
Sistema misto
Quando o ajuste é feito fora dos sistemas FURO-BASE e EIXO-BASE, o sistema chama-se misto.
Confira os tipos e exemplos de aplicação de ajustes do SFB em peças móveis (uma em relação à outra), utilizando o Sistema ISO.
Rotativo
Ajuste: H7/f7
Aplicação em peças que giram ou deslizam com boa lubrificação.
Ex.: eixos, mancais etc.
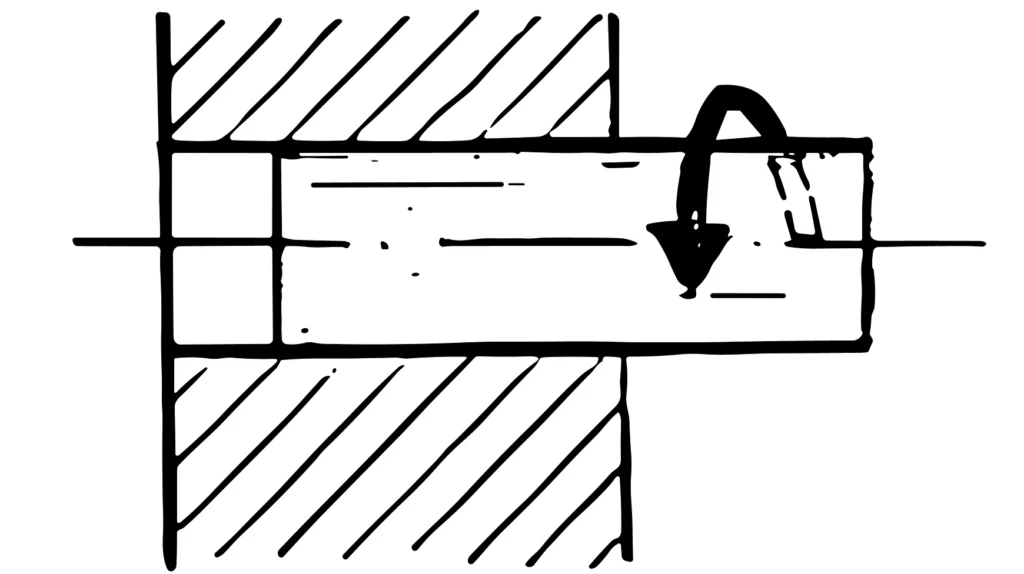
Deslizante
Ajuste: H7/g6
Aplicação em peças que giram ou deslizam com grande precisão.
Ex.: anéis de rolamento, corrediças etc.
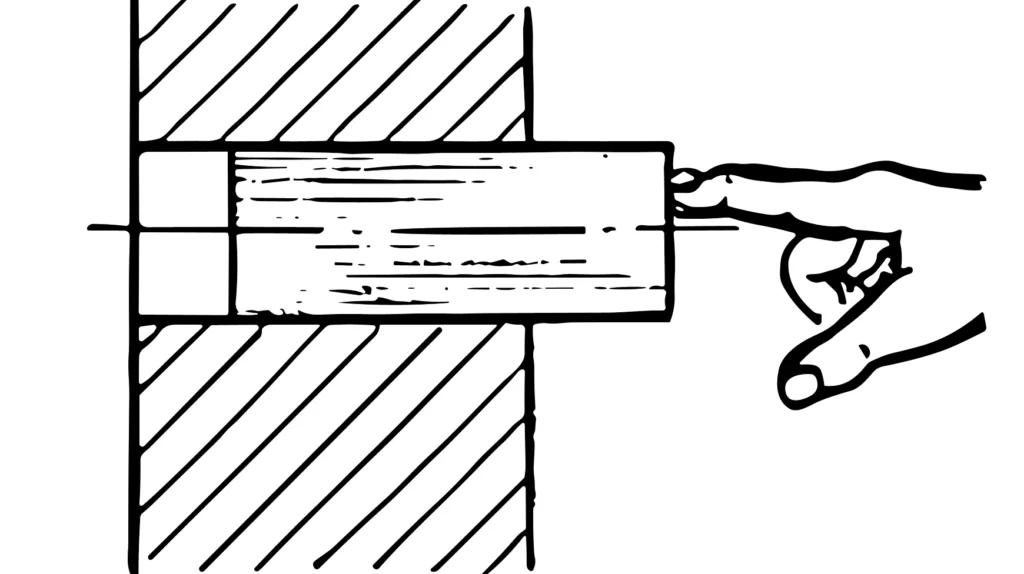
Deslizante justo
Ajuste: H7/h6
Aplicação em encaixes fixos de precisão, órgãos lubrificados deslocáveis à mão.
Ex.: punções, guias etc.
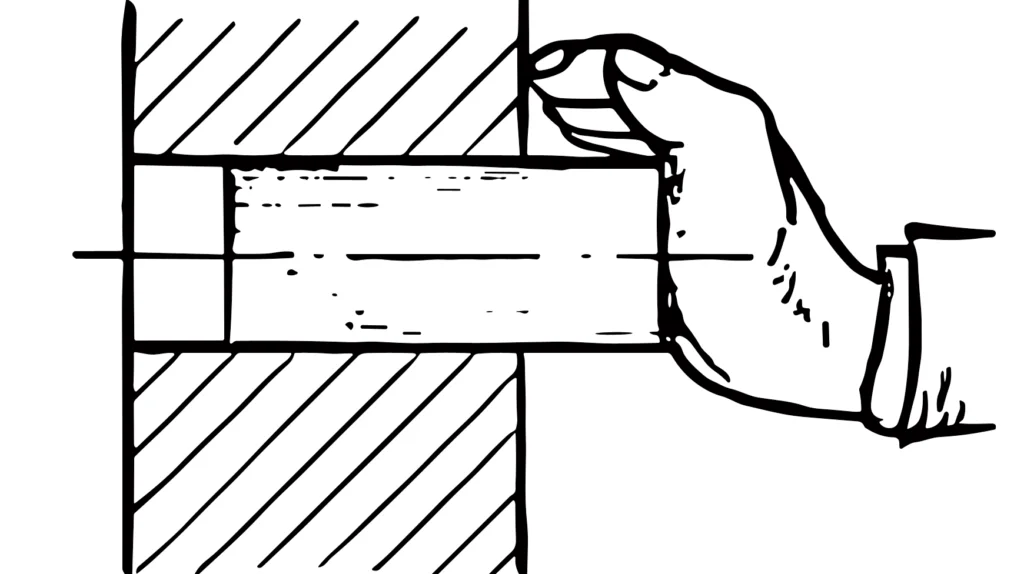
Veja os tipos e exemplos de aplicação de ajustes do SFB em peças fixas (uma em relação à outra), utilizando o Sistema ISO.
Aderente forçado leve
Ajuste: H7/j6
Aplicação em órgãos que necessitam de frequentes desmontagens.
Ex.: polias, engrenagens, rolamentos etc.
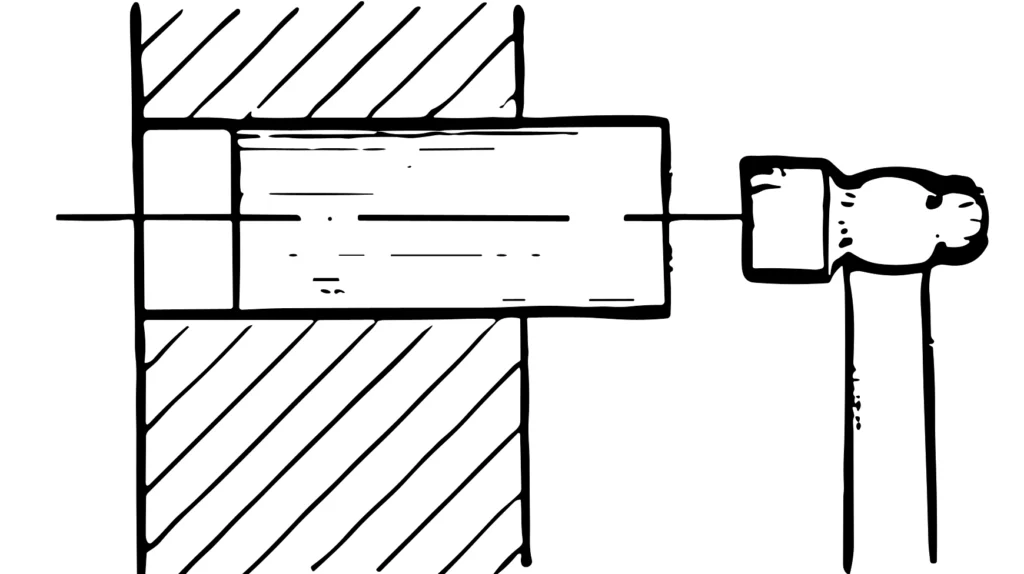
Forçado duro
Ajuste: H7/n6
Aplicação em órgãos passíveis de montagem e desmontagens sem deterioração das peças.
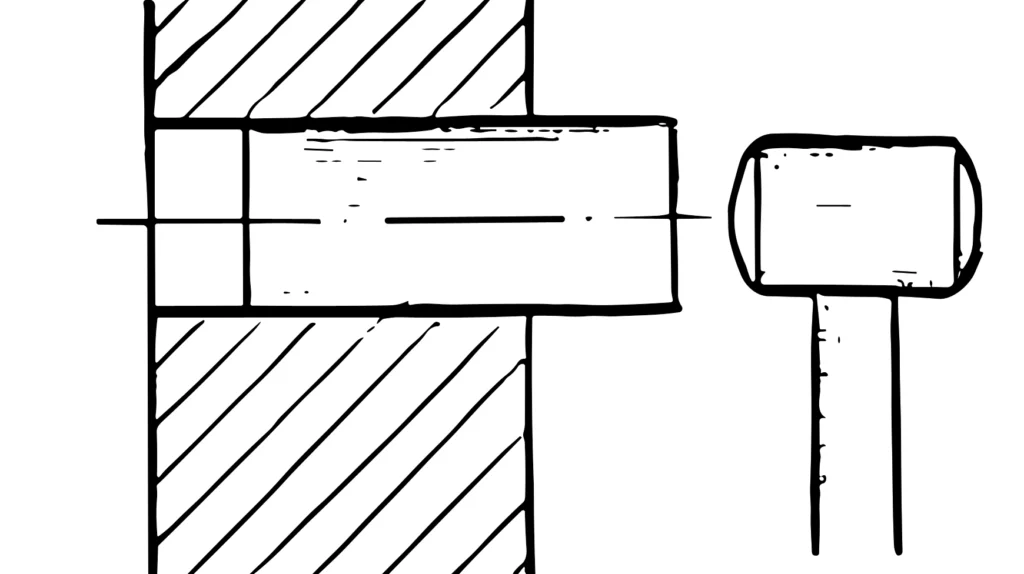
À pressão com esforço
Ajuste: H7/s6
Aplicação em peças impossíveis de serem desmontadas sem deterioração.
Ex.: buchas à pressão etc.
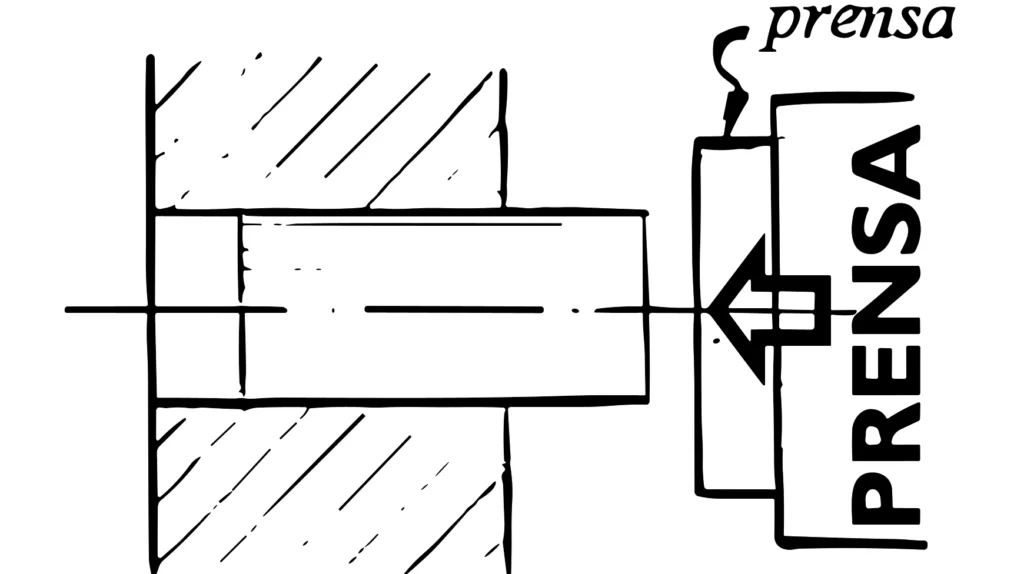
Superfícies e acabamento
O desenho técnico, além de mostrar as formas e as dimensões das peças, precisa conter outras informações para representá-las fielmente. Uma dessas informações é a indicação dos estados das superfícies das peças.
Acabamento
É o grau de rugosidade observado na superfície da peça. As superfícies apresentam-se sob diversos aspectos, a saber: em bruto, desbastadas, alisadas e polidas.
Superfície em bruto
É aquela que não é usinada, mas limpa com a eliminação de rebarbas e saliências.
Superfície desbastada
É aquela em que os sulcos deixados pela ferramenta são bastante visíveis, ou seja, a rugosidade é facilmente percebida.
Superfície alisada
É aquela em que os sulcos deixados pela ferramenta são pouco visíveis, sendo a rugosidade pouco percebida.
Superfície polida
É aquela em que os sulcos deixados pela ferramenta são imperceptíveis, sendo a rugosidade detectada somente por meio de aparelhos.
A norma NBR 8404 da ABNT, baseada na norma ISO1302, normalizou os símbolos indicativos de rugosidade da superfície para representar os graus de acabamento das superfícies. Os graus de acabamento são determinados por vários processos de trabalho e dependem das modalidades de operações e das características dos materiais usados.
O que é Rugosidade?
Rugosidades são erros microgeométricos existentes nas superfícies das peças, provenientes do processo de fabricação, tais como ranhuras, sulcos, estrias, escamas e crateras. As ranhuras e sulcos são provenientes de marcas da ferramenta durante o avanço ou posicionamento da peça no processo de usinagem. As estrias e escamas formam-se na usinagem, durante a retirada do cavaco.
O controle da rugosidade torna-se importante quando aumenta a qualidade de fabricação (tolerância dimensional pequena) ao ponto de ocorrerem irregularidades na superfície da peça maiores do que a tolerância dimensional especificada.
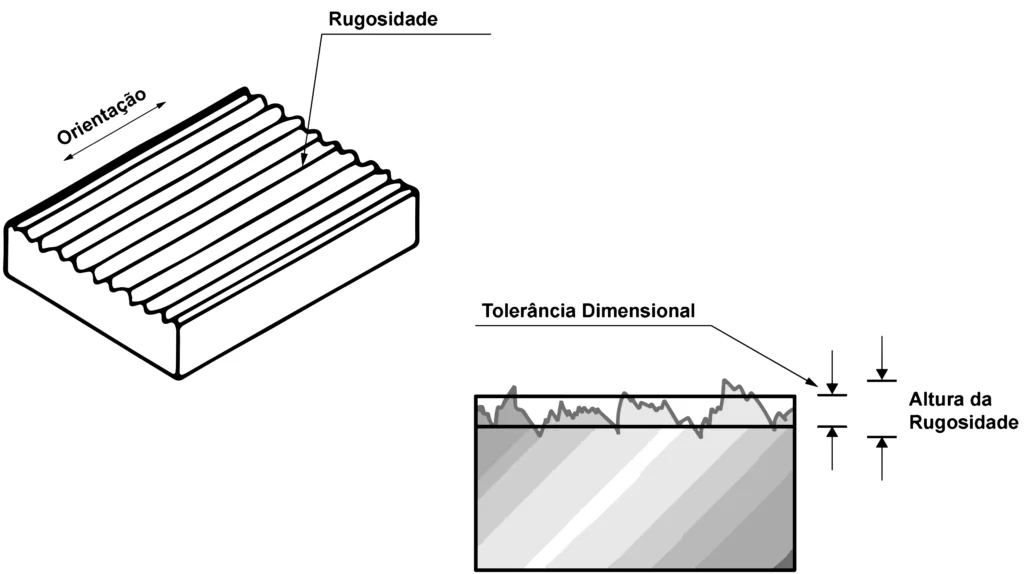
Peças que estão sujeitas a esforços intermitentes ou cíclicos, desgaste por atrito ou corrosão superficial precisam de maior controle de superfície. Quando as peças são feitas para transmitir calor, escoar fluídos, vedar ou deslizar, elas funcionam melhor.
A medição de rugosidade pode ser feita através de microscópios ou rugosímetros.
A ponta de diamante, fixada na ponta do braço do rugosímetro, percorre uma trajetória linear de comprimento “La” predefinido, captando as irregularidades existentes na superfície da peça. O rugosímetro processa as informações enviadas pelo sensor de diamante, realiza cálculos da rugosidade, apresentando um valor numérico no mostrador e/ou imprime um gráfico do perfil de rugosidade da superfície avaliada. Veja a seguir.
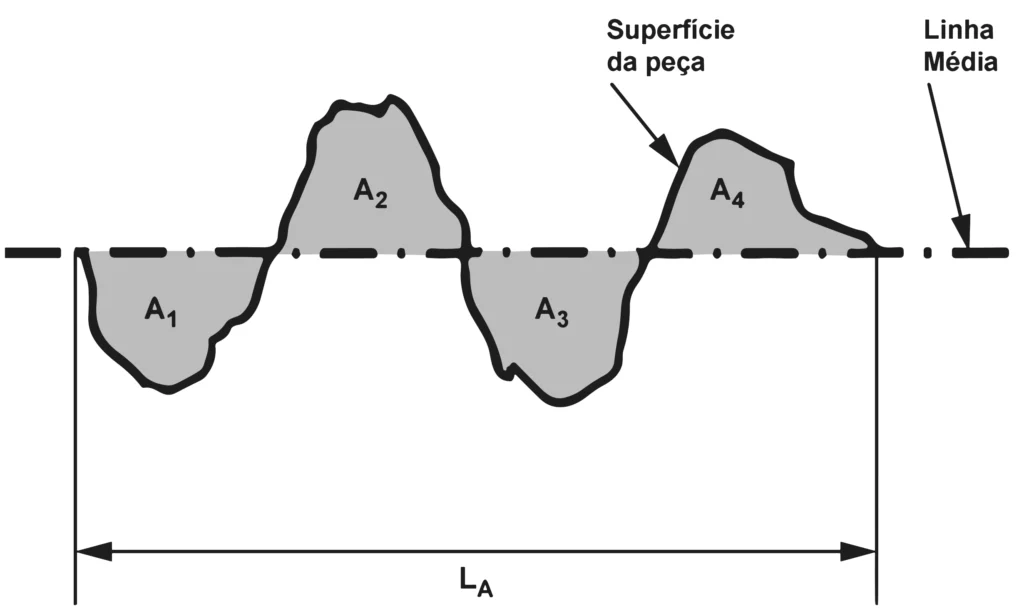
Rugosidade Média Ra é a média aritmética dos valores absolutos das ordenadas do perfil efetivo da peça em relação à linha média para um comprimento de amostragem La definido.
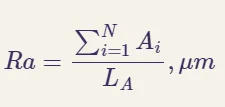
Sinais de acabamento (antigo)
De acordo com a NBR-6402, a especificação de acabamento nos desenhos por meio de sinais antigos é feita conforme a relação apresentada a seguir.
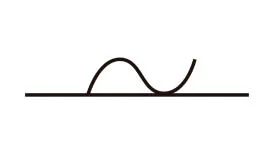
Superfície em bruto, forjada, laminada, estampada e de peças fundidas, porém com eliminação de rebarbas.
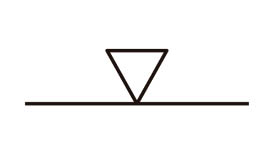
Superfície desbastada, os riscos da ferramenta são bastante visíveis. Profundidade dos sulcos 6,3 a 50µm
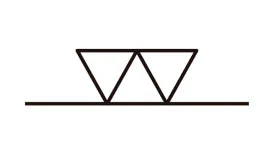
Superfície alisada, os riscos da ferramenta são pouco visíveis. Rugosidade 0,8 a 6,3µm
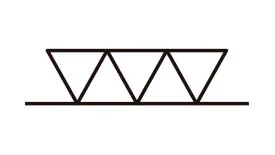
Superfície polida, os riscos da ferramenta não são visíveis. Rugosidade 0,1 a 0,8µm
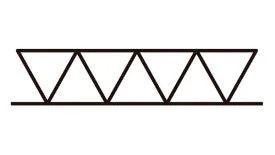
Superfície lapidada. Rugosidade máxima 0,1µm
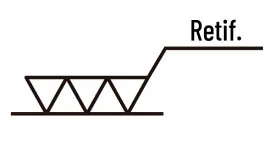
Para qualquer grau de acabamento, pode ser indicado o modo de obtê-lo.
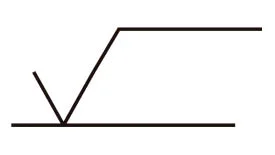
Superfície sujeita a tratamento especial indicada sobre a linha horizontal.
Sinais de acabamento (Atuais)
Também podemos observar o sinal de usinagem na representação atual de acabamento a seguir:
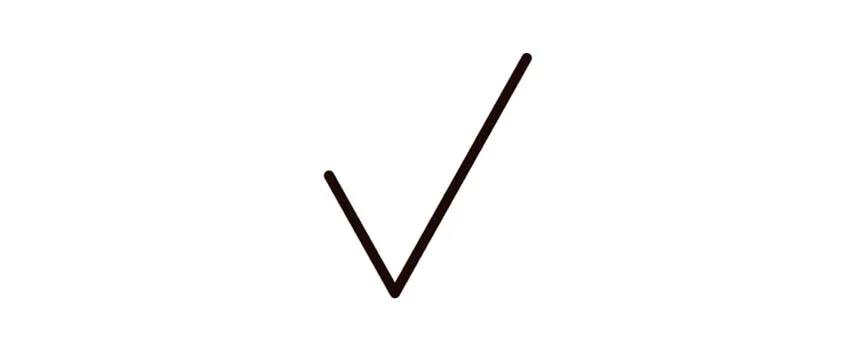
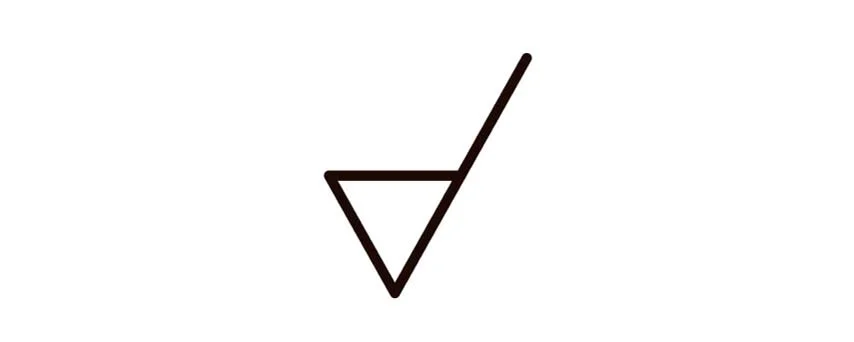
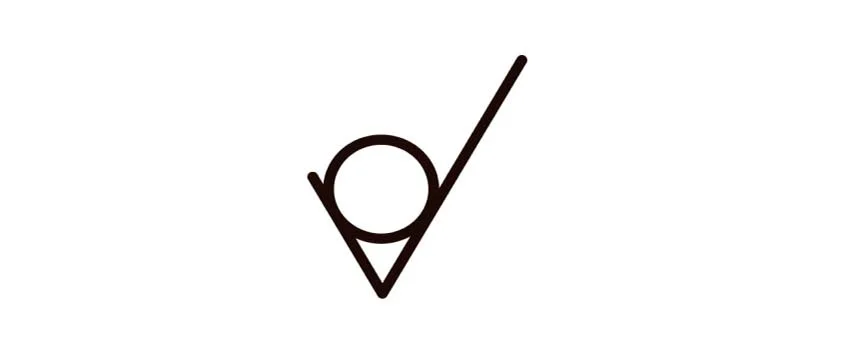
Veja a Qualidade da superfície de acabamento, baseada na norma ABNT/NBR 8004 e ISO1302.
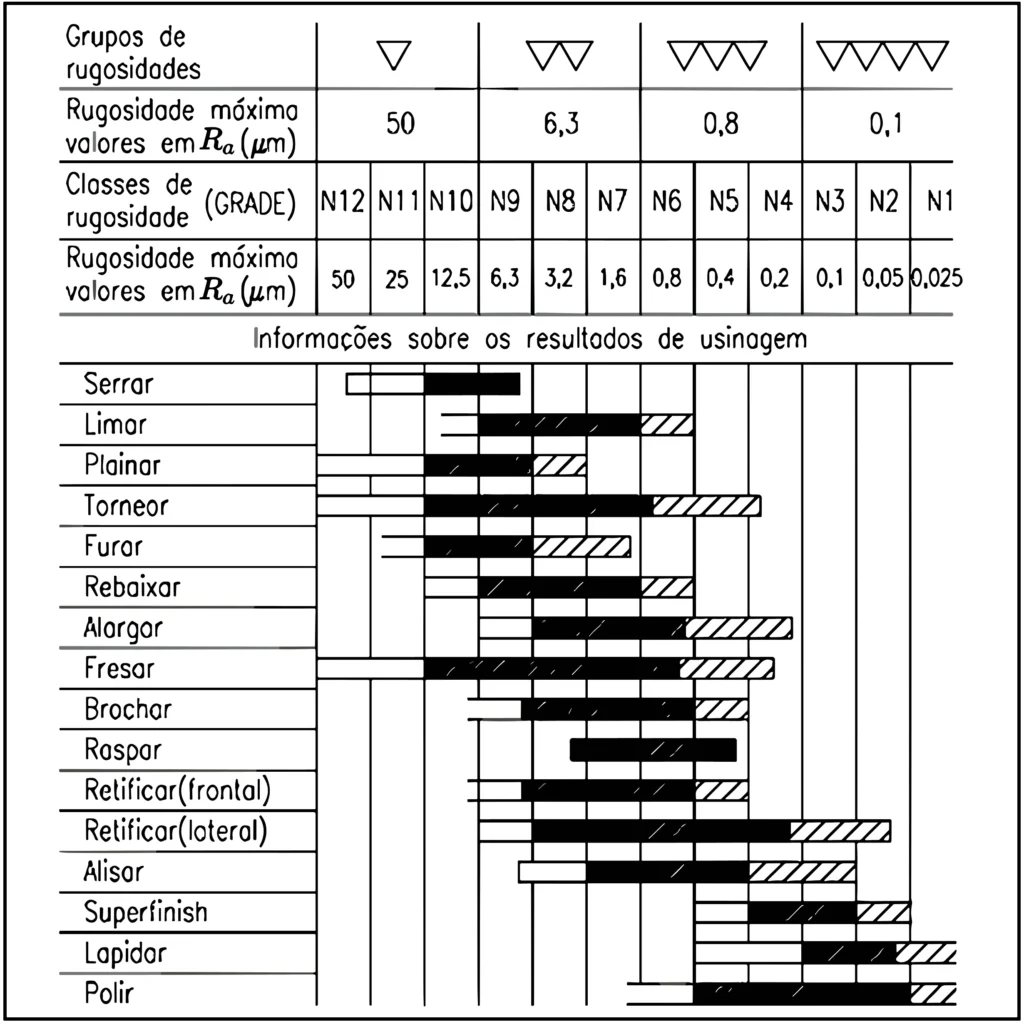
Como são representadas as informações principais e complementares de rugosidade:
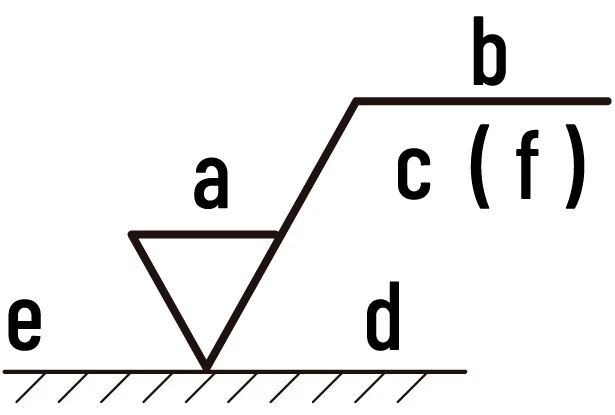
- a) Valor da rugosidade Ra, em mícrons, classe de rugosidade N1 até N12.
- b) Método de fabricação, tratamento ou revestimento.
- c) Comprimento de amostra em milímetros e
- d) Direção das estrias.
- e) Sobre metal para usinagem em mm.
- f) Outros parâmetros de rugosidade (entre parênteses).
Abaixo as indicações das características principais da rugosidade:
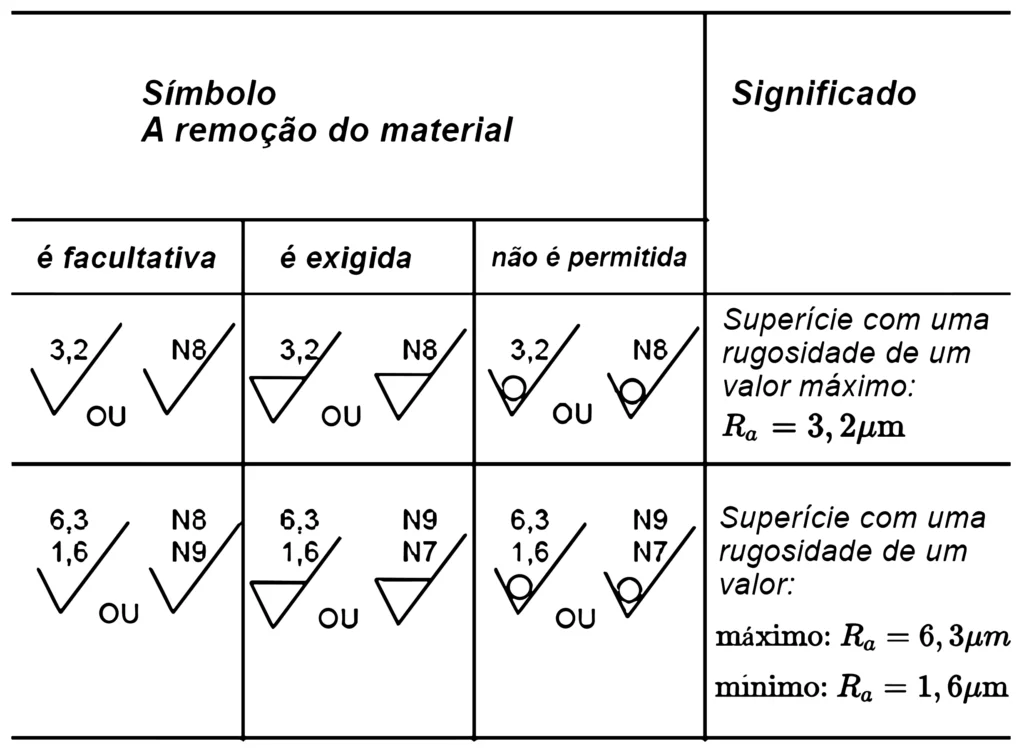
Vejamos uma relação de algumas normas utilizadas no desenho técnico mecânico fornecidas pela ABNT